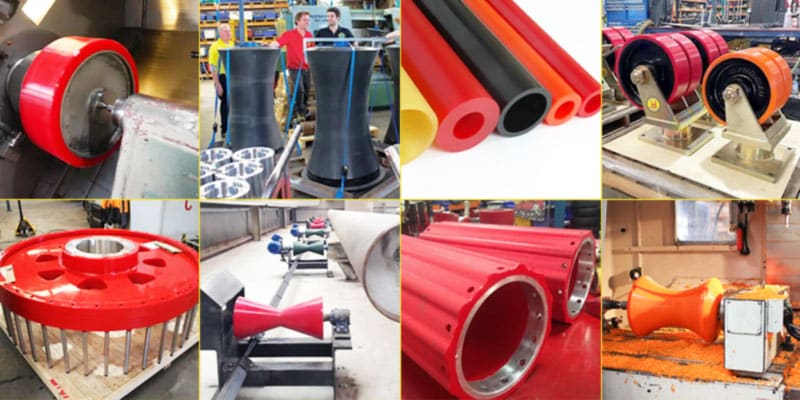
Custom Polyurethane Moulding Products and Solutions for All Industries
Our in-house team has the capability to design and manufacture bespoke polyurethane products for any application or industry.
At Richmond Rolling Solutions we’ve been customising polyurethane moving solutions for over 40 years, with leading design and manufacturing techniques that allow our team to create tailored solutions for your required application.
With the highest abrasion resistance of any polymer family, polyurethane is also the most versatile, allowing our team to make products within a broad hardness range – meaning it can be the perfect replacement for almost any rubber, injection moulded plastic or engineering plastic materials.
Our standard hardness range can cater for any application, with a wide-range of stock in-house for fast order fulfilment.
This includes 50A, 60A, 77A, 85A, 90A, 95A, 57D, 65D and 75D and standard colour options of Red, Black, Orange, Grey, Yellow and Green. Read More
Moulded Polyurethane Can Do Wonders for Your Machinery and Construction
We’re proud to cover all your PU moulding needs here at Richmond Rolling Solutions When working with something like polyurethane moulding, it’s important to source it from a seasoned, capable manufacturer. Polyurethane mouldings are not easy to create; at least, it’s not easy to make good ones. Even with the right equipment and materials, it’s important to have the right conditions and know-how surrounding the processes. It’s also essential to know which moulding process best aligns with your goals for polyurethane in the first place. In other words, you want to get your PU molding from well-equipped experts familiar with multiple methods and materials. And what better choice is there than the manufacturer that’s been serving Australians and steadily growing since 1958?
After all, we’ve worked with every machinery-intensive Australian industry there is. We know what we can offer to each one and how to best design our products to their benefit. Any seller can design a wheel or a cart, but it takes many years of dedicated service to know which wheels and carts suit equipment in hospitality, manufacturing, landscaping, or construction. You might not know for sure which of our products best suits the work you do. But we’ve worked with your industry before, and we almost certainly know more than enough to help. That’s why this is the best place to purchase custom moulded polyurethane. We know how it can benefit your machines and your construction jobs, and we can save you thousands of dollars or many tedious hours of research and guesswork. If you want a product of high quality alongside all the information you need to understand it in one convenient source, you’re with the right company.
What Is Polyurethane Mould Rubber?
Polyurethane belongs to the polymer family of plastics. Specifically, it’s an elastomeric polymer, which means that it has both high viscosity and high elasticity. That allows polyurethane to be both malleable and flexible. It can be hardened into practically any shape, and it can be made to be either totally rigid or highly flexible for the end result. Polyurethane also differs from other elastomeric polymers in its sheer versatility. You can use a wide range of methods to mould it, and it can also be produced from many different starting materials.
Calling polyurethane a plastic is like calling water a liquid. It’s correct, but it doesn’t begin to cover everything that polyurethane is or what it can do. It doesn’t just take any shape you want it to-it can also withstand some of the most extreme conditions you’d expect to see in industry. It’s resistant to all weather conditions, impact, heat, cold, corrosion, abrasion, and even radiation and UV radiation. Despite that durability, polyurethane is extremely lightweight and easy to transport as a result. Thanks to its synthetic composition, it also doesn’t truly rot or decay the way natural materials do. And because it can be made with a variety of starting compositions, it can be clear, translucent, or opaque as required. The comparison we made to water wasn’t random-polyurethane is nearly as versatile and adaptable as water.
Where Can Poly Rubber Moulding Be Applied?
Thanks to its incredible versatility, PU moulding can be used to protect surfaces, replace and surpass similar materials, and provide a strong base material for designing complex shapes. It’s widely used and appreciated in mining, agriculture, construction, food production, manufacturing, 3d printing, tech, and even in art. Our polyurethane mould making varies according to what you plan to use the moulding for.
If you want to protect machine parts that are under constant wear, you can coat them with a thin layer of PU moulding to give them a lot more longevity. Polyurethane is famously abrasion-resistant, much more so than rubber, ceramic, or even steel. It will last longer than any other protective material while still being lightweight and unobtrusive. For mining pipes and irrigation or filtration systems, polyurethane lining is a lifesaver. It prevents corrosion for years when applied evenly and thoroughly. Polyurethane can also be used to coat pulleys.
Meanwhile, in construction, PU moulding is leaving other building materials in the dust. Features such as baseboards, cornices, sunhoods, columns, plinths, and more can now be made using moulded polyurethane. It doesn’t rot or gather moisture the way wood does, which makes it superior for outdoor applications even accounting for finishing or sealing. It’s lighter than stone while being just as durable, which makes transporting and placing it easier and safer for workers. It’s stronger than plaster and brick while being just as adaptable. Odds are, your own home has several parts made of PU moulding; it’s just that useful.
Lastly, PU moulding can be used to create models and complex prototypes. It’s one of the most high-end materials used in 3D printing thanks to its incredible workability. With the right printer, you can 3D print highly intricate models with plenty of clarity and no blurring of detail. Many companies also use the material to demonstrate and test out prototypes. The material might not be cheap, but using it is often much cheaper than using a host of other materials to make a comparable prototype.
What Are Our Methods as PU Mould Manufacturers?
That depends on your needs! We provide custom moulded polyurethane for many different applications, which means we produce it in several ways. In every method, the polyurethane begins as a liquid and is mixed with a hardening agent. The mould and the polyurethane are both heated.
For very basic shapes such as pipe lining, lagging, baseboards, and columns, we use open cast moulding that enables us to make a PU pipe lining, PU lagging strips, and more. That involves either pouring liquid polyurethane into a mould or filling that mould from the bottom carefully. In either case, we fill the mould slowly to avoid any trapped air. More importantly, we choose a mould that’s made of a hydrophobic material to avoid any moisture being present, which can ruin the whole process. We commonly use aluminium or silicone for that.
To ensure the highest clarity in small details, such as in complex models and prototypes, we might use centrifugal moulding. By rapidly spinning the mould as we pour in the polyurethane, we separate the plastic from the air. Without that step, most tiny details in the finished product would be disrupted or distorted by air bubbles.
Lastly, for a variety of shapes and for high-volume jobs, you can rely on our polyurethane injection moulding. Here, we use an injector to rapidly fill a mould without any air pockets or uneven surfaces. The polyurethane here starts out in pellets, which are heated and melted as they’re pushed through the injector. This process is the only one that’s fast enough to reliably produce a high volume of products. Read Less
The perfect partner for custom polyurethane products
For specific applications Richmond Rolling Solutions can expertly manufacture polyurethane products in any hardness from 25A to 85D.
How does polyurethane compare to alternative material selections?
Compared to rubber | Compared to metal | Compared to injection moulded plastics |
Superior abrasion resistance | Abrasion resistance | High impact resistance |
Wide range or hardness for more application flexibility | Non-corrosive | Much lower tooling cost |
Lighter load bearing | Light weight | Elastic memory |
Cut and tear resistant | Flexible | Thick and thin section mouldings |
Uv and ozone resistance | Impact resistant | Noise reduction |
Lower cost tooling | Nonconductive | Lower and higher temperature range capable |
Thicker sections possible | Non sparking | Resilience |
Parts with very thick and thin sections possible | Lower cost fabrication | Elastic memory |
Colourability | Lower cost tooling compared to cast steel/iron parts | Wide range or hardness for more application flexibility |
Can be manufactured with a FRAS Rating (fire resistance & antistatic) | Noise reduction in impact applications | Abrasion resistance |
Won’t damage other steel or concrete surfaces like steel components |
What polyurethane products can we manufacture for your business?
Using precision engineering techniques and the latest equipment, Richmond Rolling Solutions can design and deliver any type of polyurethane product for your business needs!
By utilising Richmond’s in-house moulding processes we can manufacture custom shapes, hardness variability and load bearing solutions, giving us a distinct advantage over traditional suppliers across Australia.
With nearly 10,000 products in our growing range, why not talk with our design and engineering team about our custom polyurethane product solutions?
Friendly Team of Experts
In-house Engineers
Cutting Edge Fabrication Facility
Fast Turnarounds
Affordable Solutions
Contact Our Team Today!
Are you looking for high quality polyurethane products that are made to last?
Contact our experts to discuss your requirements on 1300 474 246 or email [email protected]